一、概述
传统空压机控制谈不上电控系统,一般只有电机启停控制。在空压机运行过程中,为保持输出气压稳定在一定范围内,又不使电机频繁启停,工作压力由受气压控制的机械式进气阀开启或关闭进行调节。即压力达到上限时关阀,使空气压缩机进入空载运行;压力达到下限时开阀,使空气压缩机进入满载运行。频繁的加卸载使得空压机的输出压力介于加载压力与卸载压力之间,以满足工艺的需求。而电机则一直处于工频运转状态,整套空压机的机械部件也一直处于高速运动状态。机械磨损和电力消耗是可想而知的。
传统空压机工作方式的弊病:
1、电能浪费严重:机械式空气压缩机加、卸载控制方式使得压缩气体的压力在Pmin ~ Pmax之间来回变化,Pmin是能够保证用户正常的最低压力值,Pmax是设定的最高压力值; 当空压机输出气压达到卸载压力(Pmax)时,空压机自动打开卸载阀,这时,空压机虽不需要再对压缩气体做功,但其电机仍在全速拖动整套机械系统运行,造成严重的能源浪费和系统磨损。据测空压机卸载时的功耗约占满载时的30%~50%,在卸载期间,空气压缩机做无用功,无谓地消耗能量。同时将分离罐中多余的压缩空气通过放空阀放空,造成极大的的浪费。
2、工频启动冲击电流大
虽然中、大型电机可采用Y-△减压起动,但起动电流仍然很大,对电网冲击大,易造成电网不稳以及威胁其它用电设备的运行安全。对于自发电工厂,数倍的额定电流冲击,可能导致其他设备异常,部件老化。
3、压力不稳,自动化程度底
传统空压机自动化程度低,输出压力的调节是靠对加卸载阀、调节阀的控制来实现的,调节速度慢、精度低,输出压力不稳定。
4、噪音大
持续工频高速运行,超过所需工作压力的额外压力,反复加载、卸载,都直接导致工频运行噪音大。
二、改为变频控制后的效果
1、省电:变频控制系统根据实际用气量实时调整电机转速,这样就可以有效的减少空转时间或避免空压机进入空转状态,从而大大减少能源的损失。与一般的吸入截流阀控制相比,可以节约电力30%~40%(使用空气量比为40~60%时)。
2、稳定的管网压力:变频改造后,空压机利用了变频器的无级调速特点,通过控制器的PID调节器,对压力实现快速调节控制。与工频运行的上下限开关控制相比,气压稳定性成指数级的提高。由于变频控制电动机速度精度提高,将压力变动范围控制在±0.02MPa以内,有效地提高了供气的质量。
3、 延长压缩机机械寿命: 由于变频器本身是一个软启动装置,启动电流最大在额定电流的两倍左右,与工频(星三角)启动一般在额定电流的4-6倍相比,启动冲击小。同时启动的加减速时间可调整,从而减少启动时对压缩机的电气部件和机械部件所造成的冲击,延长了压缩机,电机及其它电气,机械部件的寿命。
5、 降低空压机噪声 :一般空压机选型都按工艺最大用气量配置,而在实际生产过程中,实际用气需求经常达不到最大供气量。 变频器根据实际用气需要调节电机转速,机械转动噪音随之变小,且免去机械式阀门的频繁动作,进一步降低生产噪音,同时变频器有规避机组共振点的作用,既保护了设备,又进一步降低噪音。
三、技改实测数据
以75KW 主机为例
工频加载电流:148A 卸载空转电流:69A;
变频加载电流:135A,恒压时电流20~135A之间调节,卸载电流:10A以下。
实测记录:工频运行一天(24小时),加载时间共计15小时,卸载时间9小时,耗电为15×75度+9×35度=1440度电;
同样工况变频运行一天(24小时),全天PID恒压工作,实测耗电979度电。
结果:省电460度,按电价0.5元计算,折合省电费230元/日,每年按300天工作计算,
300天×230元/天=69000元。
变频改造成本未超过69000元。
四、系统配置方案
1、空压机专用变频器 75KW 一台
2、专用控制器 一套
3、断路器、接触器等低压元件 一批
4、控制柜 一套
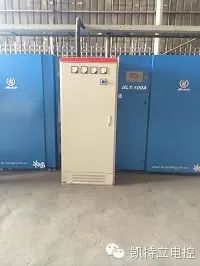
(具体型号及参数请致电400-0871-559咨询)
五、工程实景
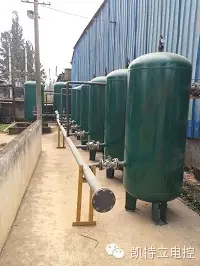
气罐区
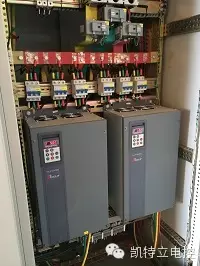
低压螺杆空压机两台
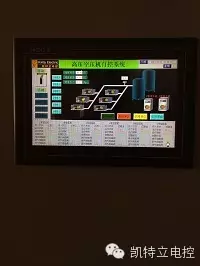
人机界面
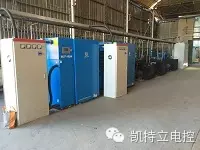
两台螺杆机+六台增压机+4台冷干机
增压机用的变频器六台